Why Expansion Joints for Pipelines Are Critical to Industrial Systems
This blog explores the importance of expansion joints in industrial pipeline systems. It explains their function, types, benefits, real-world applications, and how they contribute to system efficiency and safety. It includes a focus on selecting the right product based on operating conditions and engineering requirements.
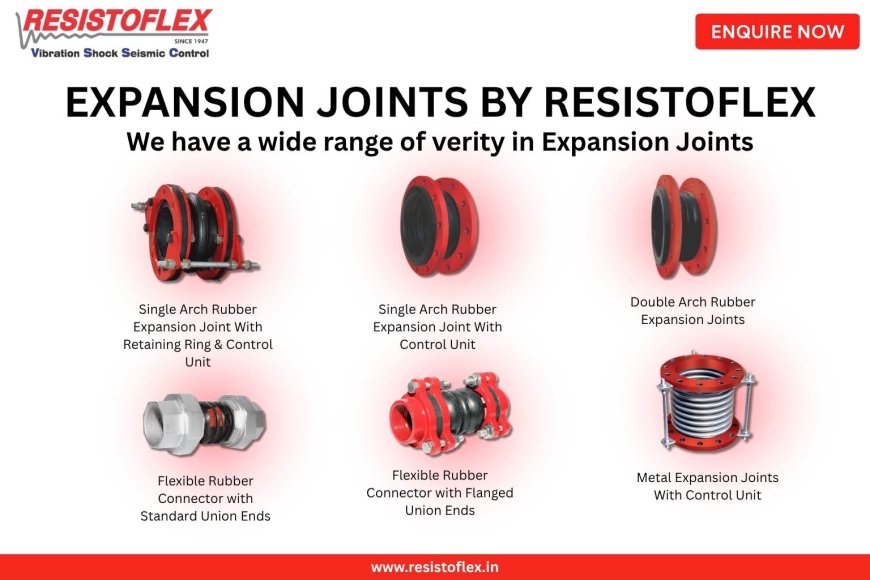
In industrial piping systems, reliability and flexibility are essential to long-term performance. When pipes are exposed to fluctuating temperatures, pressure variations, or dynamic forces, failure points can quickly emerge. To prevent structural damage and costly downtime, engineers rely on a vital component: expansion joints for pipelines.
These joints play a crucial role in absorbing movement, reducing stress, and maintaining the integrity of the piping infrastructure. While they may seem like a small addition, their impact on safety and system efficiency is significant.
What Are Expansion Joints and Why Are They Important?
Expansion joints are flexible connectors that absorb thermal expansion, vibration, misalignment, and other mechanical movements in pipelines. Without them, the rigid nature of metal or concrete piping would lead to stress fractures, leaks, or complete failure.
In systems where hot fluids, steam, or gases are transported, pipeline materials expand and contract. Expansion joints for pipelines act as buffers, accommodating this movement without transferring stress to other parts of the system.
Types of Expansion Joints for Industrial Pipelines
Various types of expansion joints are used in pipeline systems, each tailored to specific applications:
-
Metal Expansion Joints: Suitable for high-temperature and high-pressure conditions.
-
Rubber Expansion Joints: Ideal for noise and vibration dampening, commonly used in HVAC, water, and pump systems.
-
Fabric Expansion Joints: Best suited for air and gas ducts in industries like power generation and cement plants.
Each type is selected based on factors such as operating temperature, pressure range, movement type, and installation environment.
Key Benefits of Expansion Joints in Pipeline Systems
1. Absorb Thermal and Mechanical Movement
Expansion joints compensate for axial, lateral, and angular movement caused by temperature variations or system operation. This protects pipes and adjoining equipment from stress and deformation.
2. Extend Equipment Life
By isolating movement and reducing mechanical load, expansion joints help prevent wear and fatigue on pumps, compressors, and connected structures.
3. Minimize Noise and Vibration
Rubber expansion joints absorb vibrations and reduce noise, particularly in systems involving pumps or rotating equipment.
4. Prevent System Failures
In the absence of expansion joints, pipelines are vulnerable to cracks, joint separation, and collapse—leading to expensive repairs and operational disruptions.
Typical Applications of Expansion Joints for Pipelines
Expansion joints for pipelines are used in a wide range of industries and systems:
-
Power Plants: Steam and high-temperature fluid transport lines.
-
HVAC Systems: Chilled water and hot air lines.
-
Chemical and Process Industries: Handling corrosive or high-pressure fluids.
-
Water Treatment Plants: Pump and pipeline vibration isolation.
-
Oil & Gas: Absorbing thermal growth and movement in transfer lines.
Their use is integral wherever pipeline stability, longevity, and safety are priorities.
Choosing the Right Expansion Joint
Correct product selection depends on understanding movement requirements, media compatibility, operating temperature and pressure, and installation limitations. Choosing an unsuitable joint can lead to premature failure, leakage, or structural stress.
At Resistoflex, our technical team supports clients through specification, customization, and post-installation guidance, ensuring optimal performance for each project.
Conclusion
Expansion joints are more than a protective accessory—they are a core element in the design of modern, efficient, and durable piping systems. By managing thermal growth, reducing vibration, and safeguarding structural integrity, they enhance both performance and safety.
Whether for HVAC systems, chemical processing lines, or high-temperature applications, investing in the right expansion joints for pipelines delivers long-term operational reliability and peace of mind.