Ferric Sulfate Production Cost Report and Market Insights
Procurement Resource, a globally trusted provider of market intelligence and procurement analytics, is proud to release its latest Ferric Sulfate Production Cost Report.
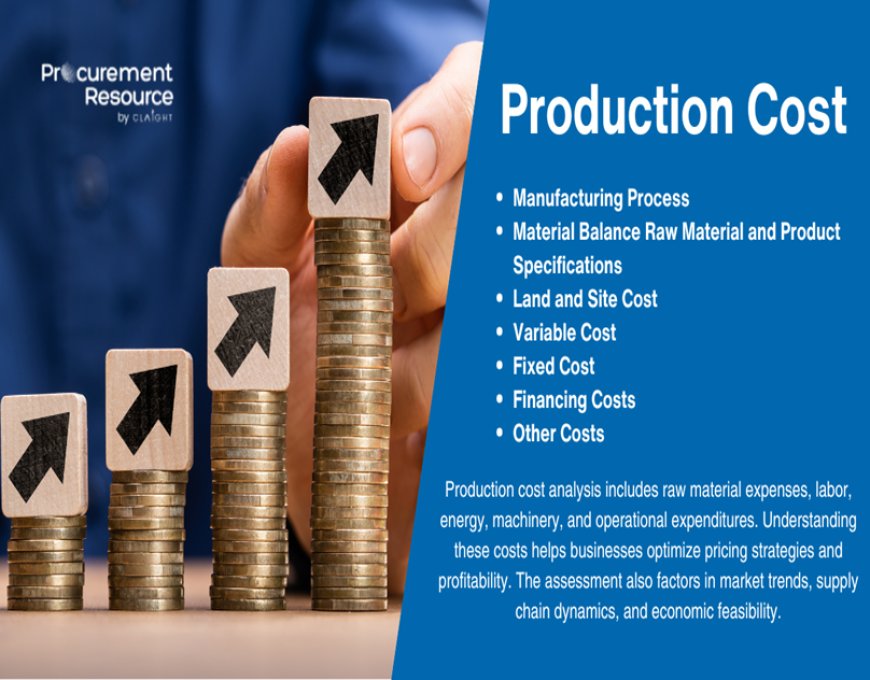
Procurement Resource, a globally trusted provider of market intelligence and procurement analytics, is proud to release its latest Ferric Sulfate Production Cost Report. This detailed report is an essential tool for manufacturers, procurement strategists, water treatment companies, and industrial investors seeking in-depth knowledge of ferric sulfate's production economics, market behavior, and investment opportunities.
Ferric Sulfate: An Essential Inorganic Chemical
Ferric sulfate (Fe₂(SO₄)₃) is a yellow to reddish-brown solid or solution primarily used as a coagulant in water and wastewater treatment. Known for its effectiveness in removing suspended solids, phosphorus, and heavy metals, it plays a critical role in municipal, industrial, and mining operations. Additionally, ferric sulfate is used in the electronics, pigments, and etching industries.
Its growing applications across environmental and industrial domains make it a strategically important chemical in the global supply chain.
Applications of Ferric Sulfate
- Water Treatment: Municipal and industrial effluent clarification
- Sludge Conditioning: Dewatering and volume reduction
- Pigments: Precursor for iron oxide pigments
- Electronics Industry: Etchant for printed circuit boards
- Catalysis and Oxidation: Intermediate in various chemical syntheses
Why This Report Matters
This report by Procurement Resource delivers a thorough cost analysis, guiding stakeholders through:
- Capital and operational expenditure
- Raw material and utility cost trends
- Manufacturing process insights
- Market pricing, ROI, and break-even projections
- Environmental and regulatory considerations
It is designed to support business expansion, procurement planning, and market entry strategies.
Production Methods Covered in the Report
The report explores two primary commercial production routes of ferric sulfate:
1. Direct Reaction Method (Using Ferric Oxide or Iron Scraps)
In this process, iron or ferric oxide is reacted with sulfuric acid in the presence of an oxidizing agent like chlorine or hydrogen peroxide.
Chemical Reaction:
Fe₂O₃ + 3H₂SO₄ → Fe₂(SO₄)₃ + 3H₂O
2. Roasting and Leaching of Pyrite or Iron Sulfide Ores
An indirect route involving the oxidation of pyrite (FeS₂) followed by leaching and purification. This is typically used when ferric sulfate is produced as a by-product or integrated with sulfuric acid production.
Each process route involves different cost structures, raw material inputs, and environmental compliance standards. The report presents a side-by-side cost comparison of these methods.
Raw Material and Utility Cost Breakdown
Key Raw Materials:
- Iron scraps or ferric oxide
- Concentrated sulfuric acid
- Oxidizing agents (e.g., chlorine gas, hydrogen peroxide)
- Water
Utility Requirements:
- Electricity: For heating, mixing, and pumping
- Steam: Required in some wet reaction and distillation setups
- Cooling water: For process control and safe operation
The report provides real-time cost tracking of these inputs in major production regions (North America, Europe, and Asia-Pacific), highlighting price volatility and supply chain risks.
Production Infrastructure and Technology Requirements
The setup of a ferric sulfate production facility requires the following:
1. Core Processing Units:
- Reactor vessels (glass-lined or stainless steel)
- Acid-resistant pumps and piping
- Settlers or filtration units
- Storage tanks (for both reactants and product)
2. Safety and Environmental Controls:
- Fume scrubbers and gas handling systems
- Effluent neutralization units
- Corrosion-resistant materials for all contact surfaces
3. Optional Add-ons:
- Drying equipment (for solid ferric sulfate production)
- Crystallization units (for high-purity applications)
The report provides CAPEX estimates based on plant capacity (small-scale, mid-scale, and industrial-scale setups).
Step-by-Step Process Overview
Typical Ferric Sulfate Solution Production via Iron and Sulfuric Acid:
- Raw Material Preparation:
Iron scraps or ferric oxide are screened and cleaned. - Reaction Stage:
Sulfuric acid is added in controlled quantities in a reactor vessel. The mixture is heated and stirred. - Oxidation Stage:
Oxidizing agents (e.g., chlorine or H₂O₂) are introduced to fully convert iron(II) sulfate to ferric sulfate. - Purification:
The resulting solution is filtered or settled to remove insoluble impurities. - Storage or Drying:
The product is either stored as a liquid (most common for water treatment) or dried for powder applications.
The report outlines each process stage along with associated costs and energy consumption.
Cost Analysis: Ferric Sulfate Production
Cost Categories Considered:
Cost Component | Description |
---|---|
Raw Material Costs | Sulfuric acid, iron, oxidizing agents |
Utilities | Energy for heating, cooling, and pumping |
Labor Costs | Operators, technicians, quality control |
Maintenance | Equipment upkeep, corrosion prevention |
Waste Disposal | Effluent treatment, sludge handling |
Overheads | Safety, compliance, logistics |
Estimated Production Cost per Metric Ton (Solution Form):
Region | Estimated Cost (USD/MT) |
---|---|
North America | $180–$250 |
Europe | $200–$280 |
Asia-Pacific | $140–$210 |
Costs vary depending on feedstock type, scale, and energy prices.
Market Pricing Trends and Demand Outlook
Ferric sulfate prices are influenced by:
- Sulfuric acid prices (linked to sulfur and oil markets)
- Scrap iron availability
- Seasonal demand from water treatment utilities
- Regulatory pressure on heavy metal removal
Pricing Benchmarks:
- Liquid ferric sulfate (40% solution): $250–$400/MT depending on purity and volume
- Solid ferric sulfate: Higher cost due to drying and packaging
Demand is forecasted to grow at a CAGR of ~4–5% globally, with developing countries increasing investments in wastewater and drinking water infrastructure.
Environmental Compliance and Safety
Ferric sulfate production requires strict environmental and occupational compliance due to:
- Corrosive and acidic inputs
- Potential emissions (e.g., SO₂, chlorine vapors)
- Waste sludge management
Key Standards to Follow:
- OSHA/REACH/GHS regulations
- Local water and air emission permits
- Waste handling under hazardous material codes
The report outlines costs and best practices for ensuring regulatory adherence and worker safety.
Profitability and Financial Indicators
The report includes:
- ROI and IRR calculations
- Payback periods (typically 2–5 years depending on scale)
- Break-even volumes and price sensitivity analysis
Profitability can be enhanced through:
- Vertical integration with sulfuric acid plants
- Securing long-term contracts with municipal bodies
- Using by-products or waste heat for additional revenue streams
Sustainability and Future Outlook
With rising focus on water quality, ferric sulfate is gaining favor over alum (aluminum sulfate) due to:
- Lower residuals in treated water
- Greater phosphorus removal efficiency
- Lower environmental impact in sludge
There’s growing research on green production techniques, including:
- Use of recycled iron from industrial waste
- Electrochemical oxidation instead of chemical oxidants
The report evaluates these emerging technologies and their impact on production cost and environmental scorecards.
Why Choose Procurement Resource?
At Procurement Resource, we combine technical expertise, global market tracking, and proprietary cost modeling to deliver reports that offer:
- End-to-end cost breakdowns
- Comparative regional production analysis
- Real-time pricing data
- Operational and capital planning insights
We enable businesses to make profitable, sustainable, and scalable production decisions in a competitive marketplace.
Request a Free Sample Report
Interested in exploring the Ferric Sulfate Production Cost Report in full?
Request a Free Sample Report Here – https://www.procurementresource.com/production-cost-report-store/ferric-sulfate/request-sample
Contact Information
Company Name: Procurement Resource
Contact Person: Ashish Sharma (Sales Representative)
Email: sales@procurementresource.com
Location: 30 North Gould Street, Sheridan, WY 82801, USA
Phone:
USA: +1 307 363 1045
UK: +44 7537171117
Asia-Pacific (APAC): +91 1203185500